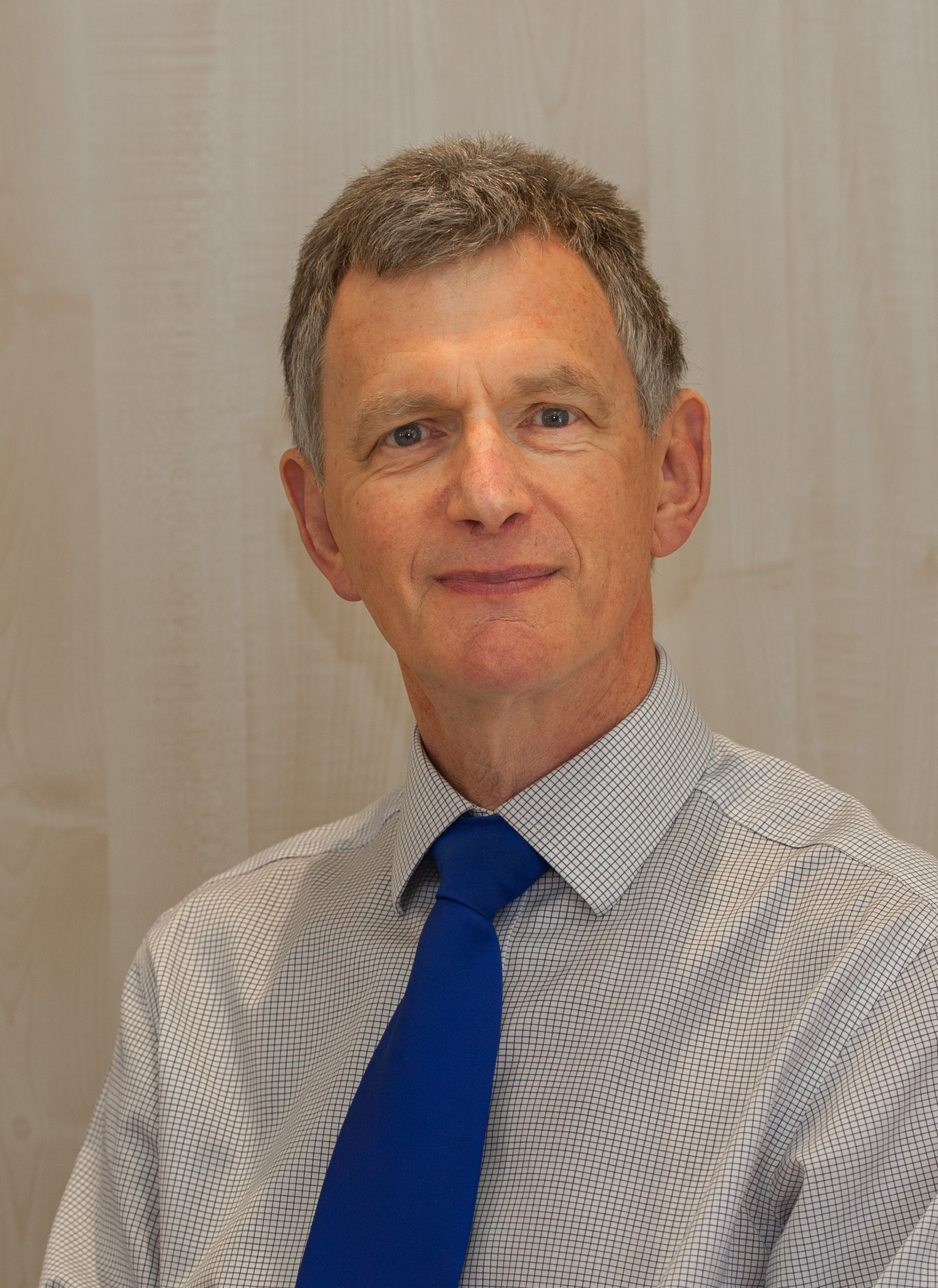
Staff stories: Richard Graveling, Principal Ergonomist
#IOM50
#IOM50
In the following years there was scarcely any part of the coal mining process that we didn’t research in some way. Before any coal can be mined, “roadways” had to be dug through the strata to reach it and, depending on the type of mining, had to be kept up with the advancement of the coalface as the coal was removed. Massive machines were used to cut some of these roadways, or holes were drilled and explosives used to cut them out. Studies of these road-heading machines and all the associated physical activities (such as erecting roof supports) formed part of our work. Once a coalface was operational, machines called shearers were most commonly used to cut the coal, and again, the design of these came under our scrutiny.
Advancing a roadway needed a constant supply of material such as the supporting girders or the sheets of corrugated iron used to cover their walls and ceiling. Manual handling of mining supplies formed another project (and if anybody want to know what part condoms took in that work just ask!).
Once the coal was brought out of the pit it was taken to a coal preparation plant and, you guessed, we worked in those as well. Or if it wasn’t brought out immediately it might be stored in huge underground bunkers. Unfortunately, internal maintenance of these resulted in a number of fatalities – so the ergonomics of this maintenance work featured again.
Aspects of the mining environment also came under our scrutiny: communication in noisy environments; mine lighting; powered helmet respirators for dust protection; and the warm humid environments in some mines were added to our portfolio. As with all our projects, that provided some memorable moments – such as the coalminer wearing nothing but his pit boots, belt and safety helmet straddling a conveyor belt and smashing an overlarge lump of rock that was blocking it (with rock splinters flying everywhere). The irony is that the worst conditions we looked at (and they were considered bad) were actually about the same as a warm summer day in Singapore.
Believe it or not there were more projects in other areas – and as you can imagine a wealth of memories. However, I will finish with how I managed to get the IOM banned (luckily only temporarily) from an entire coalmining area. I had learned that a colliery in that Area had a programme running to train selected miners in the ‘old’ manual methods – to provide a reserve capability when mechanised system failed. We felt this offered a fantastic opportunity to study the physical workload associated with these. However, before launching any formal request I decided to phone the colliery to check the story (which turned out to be false). As I saw it, I thanked the Colliery Manager for speaking to me and said ‘that I wouldn’t be troubling him any further’. But! It seems that word of this approach was passed up to the Area Director who flew into a range at the audacity of someone “trying to work in one of his pits without his permission”. As a result he banned the PFR workers (or any other IOM staff) from his Area. A seemingly innocent quick call to check my facts blew up in my face in spectacular fashion and taught me an important lesson.
I can’t possibly shoehorn all the memories and anecdotes from these ten or so years into this space – and of course that was just the beginning. A whole new chapter in the new IOM lay ahead – but that as they say is another story.
P.S Anyone interested in knowing more about our coalmining years do get in touch.